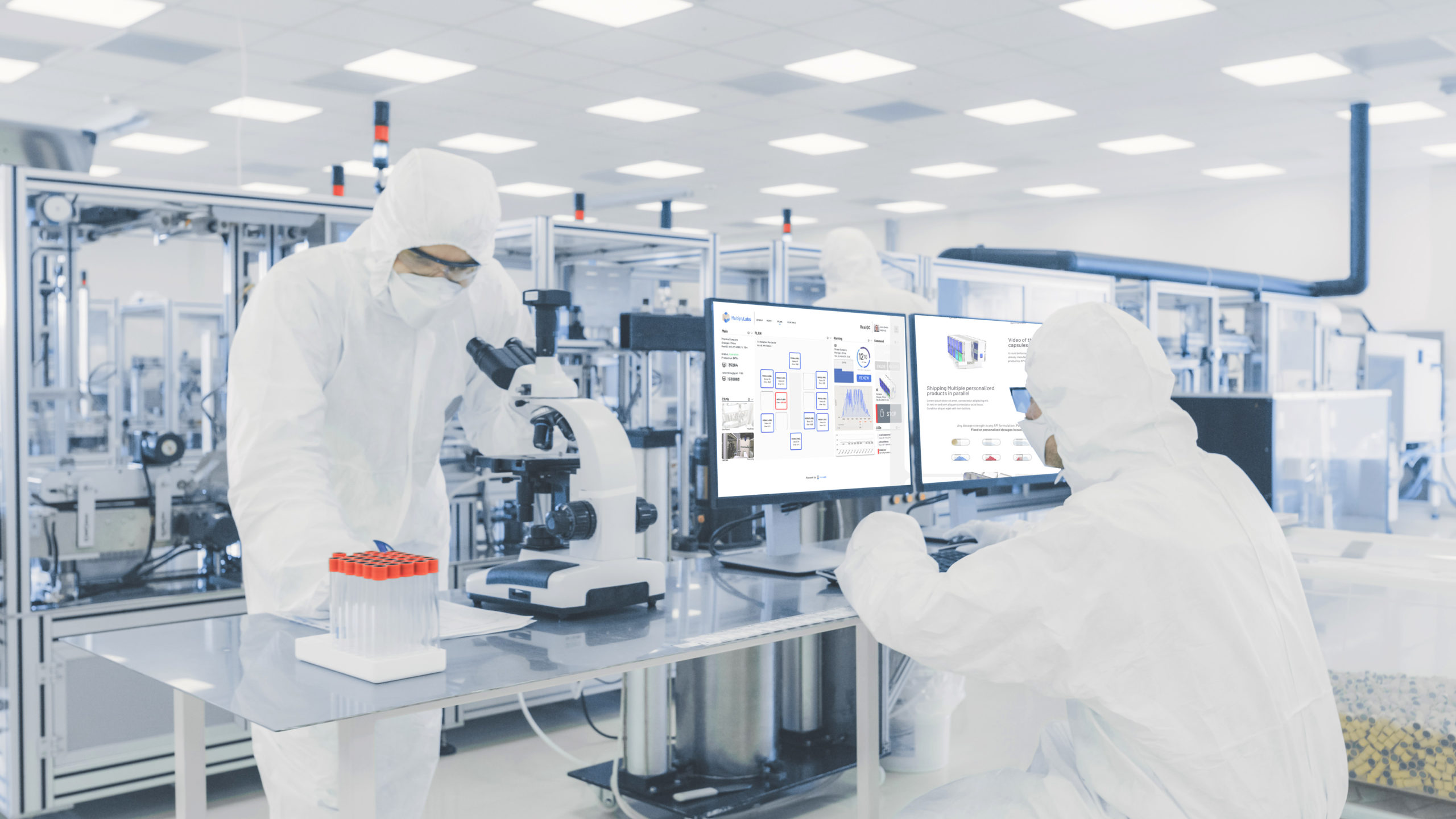
Digital Process Control: Digital QC
Digital QC is Multiply Labs’ automation software. It enables process planning for the robotic systems, and it creates comprehensive digital records for every drug product. Digital QC is CFR Part 11 compliant, and it works both on-premises and in the cloud. Discover the unique features of our digital quality system:
- Automated data collection
Digital QC automatically collects a comprehensive set of digital process data.
Data are logged and stored by validated software systems. - 100% traceability
Our validated software systems store the timestamp and ID of each manufacturing process task, creating a secure & reviewable audit trail. - Paradigm shift to in-process QC
An unprecedented amount of process data is measured and stored by Digital QC.
This enabling a paradigm shift from traditional (post-process) to advanced (in-process) QC approaches.
Digital records
Digital QC measures and stores an unprecedented level of in-process data. This digital information is automatically handled by validated software systems, meeting or exceeding CFR Part 11 compliance requirements.
Digital records include critical process parameters required by our customers. New sensors and instruments can be added to monitor the process even more accurately. The volume of data managed by Digital QC would be impossible to handle with manual quality approaches.
Multiply Labs’ data systems are compatible with the leading GxP software systems for facility and data management.
This video shows how Digital QC automatically creates Digital Records in real time, filling a human-understandable document.
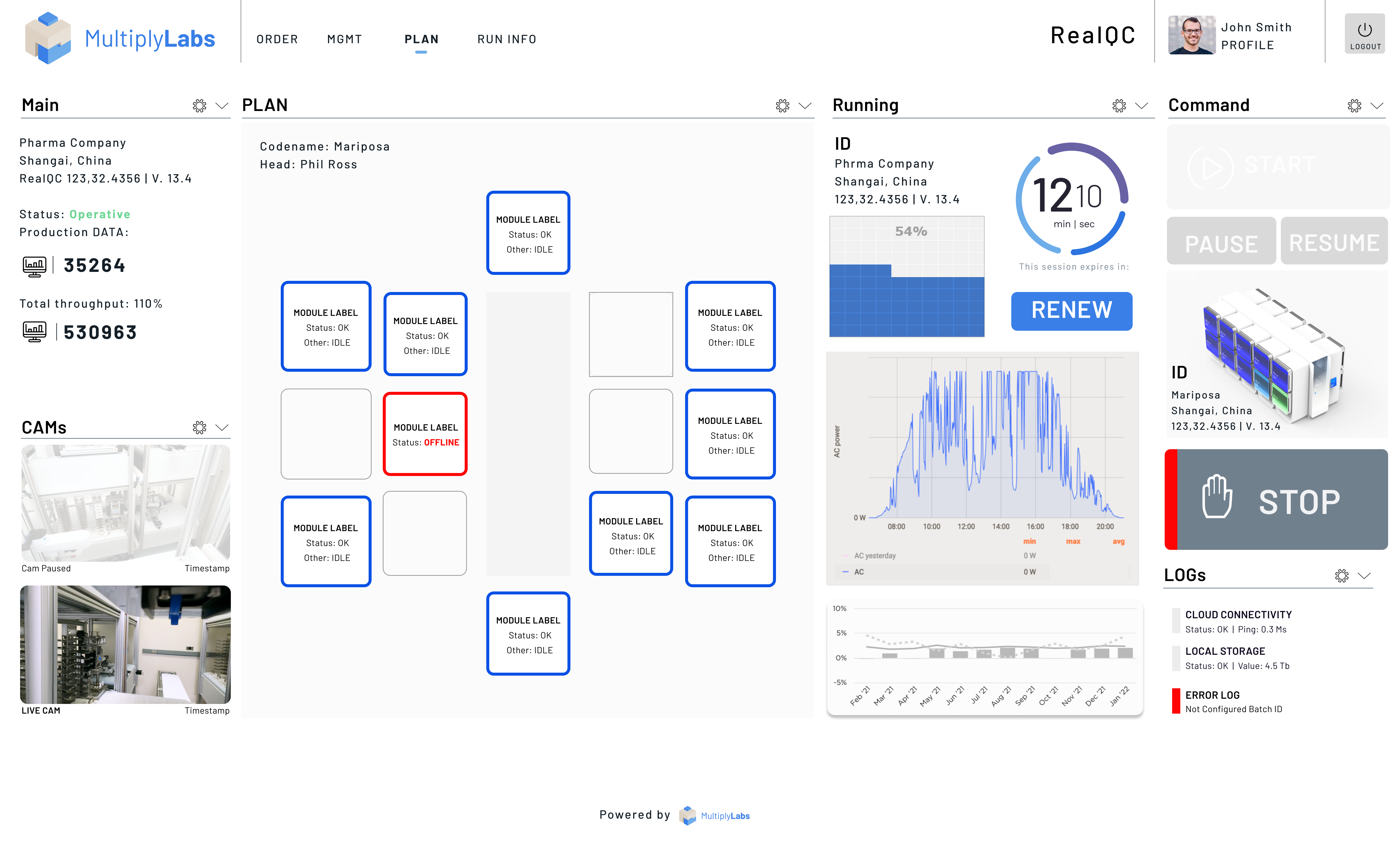
The Dashboard
The Dashboard is the on-premises operator interface for Multiply Labs’ robotic systems. It was developed to allow our customers’ manufacturing teams to:
Schedule new manufacturing jobs.
Set the process parameters of new manufacturing jobs.
Monitor the status of the robotic system in real-time.
The Planner
The Planner is the “brain” of the robotic system. When a manufacturing job is entered in the system, the Planner allocates the various steps of the process to the modules in the robotic system. The robots then execute the plan and communicate its status to the operators through the Dashboard.
The Planner is designed to maximize the efficiency of the robotic systems. It enables:
- Parallelism
Create plans that maximize system utilization – for example, by using multiple “slow” modules (e.g. bioreactors) at the same time. - Flexibility
Adapt the plan to a different set of robotic modules, e.g. when new modules are added. - Throughput
Manufacture multiple drug products at the same time for maximum throughput. ...and many more precision medicine use cases!
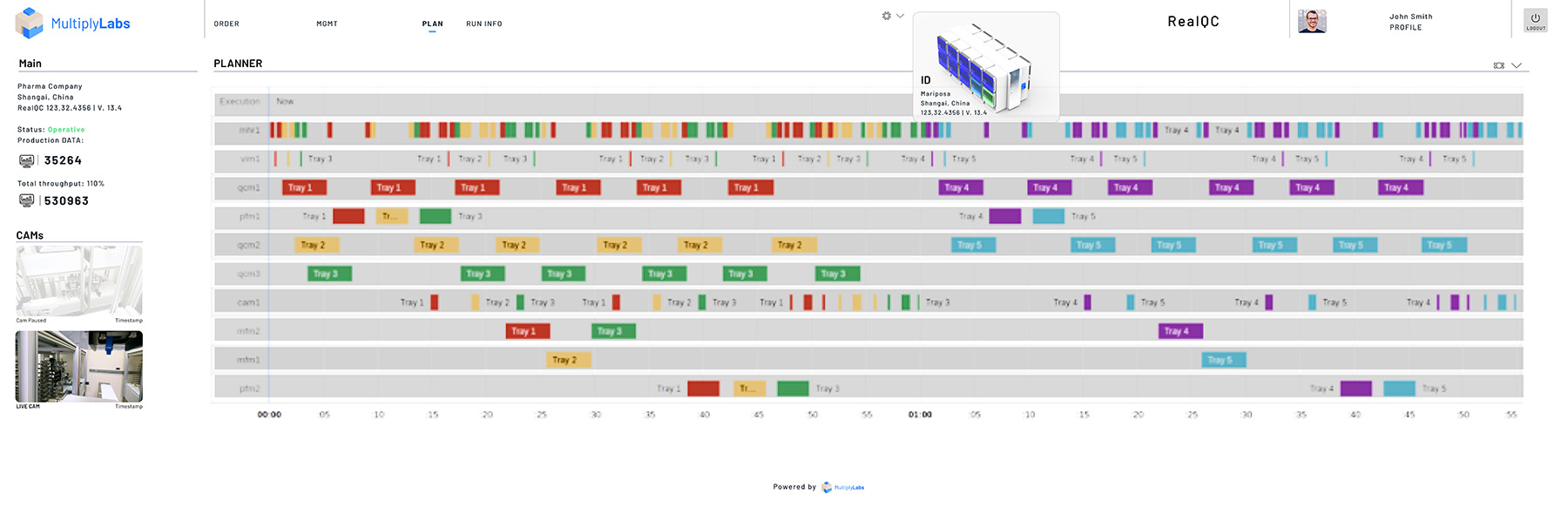